—by Matt Milkovich

5 years in the past, when Renfu Lu’s analysis crew examined its in-field sorting machine in Michigan apple orchards, they obtained suggestions from growers, and a few steered that as a substitute of people feeding apples into the sorter, why not add a robotic harvester and create a totally automated choosing and sorting system?
So, Lu, a analysis chief with the U.S. Division of Agriculture’s Agricultural Analysis Service, and his Michigan State College collaborators went again to the drafting board to design a extra formidable machine. This fall, they had been again at Schwallier’s Nation Basket in Sparta to show their robotic harvester prototype. Inside the subsequent 5 years, they plan to have a commercially viable, absolutely automated cellular platform that may harvest apples and type them within the area.
“There are nonetheless main technical points to beat, however I’m assured we are able to meet that aim,” Lu stated. “Yearly will see important enhancements in efficiency.”
Lu mentioned the venture’s subsequent steps through the September demonstration. He plans to energy the platform by electrical battery. He needs every two-armed robotic module to achieve a choosing velocity of two to three seconds per fruit, roughly the equal of human pickers.
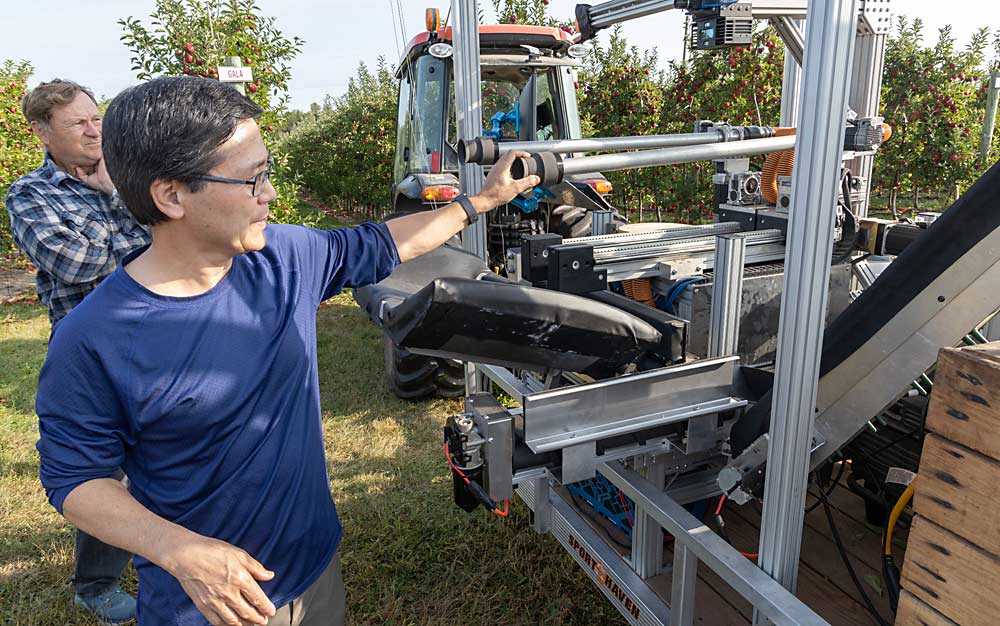
“Our single-arm robotic module has reached a choosing velocity of three.5 seconds per fruit, so we really feel assured that our two-arm robotic module can attain the goal choosing velocity after the system is additional optimized,” he stated.
The demo harvester was pulled by a tractor. A graduate pupil used a laptop computer to regulate the platform’s peak and displacement. The crew ran the manipulation arms at 60 % of their most velocity. MSU mechanical engineering professor Zhaojian Li expects the harvester to be absolutely automated by subsequent season.
The venture obtained a four-year, $3.5 million grant from the USDA’s Specialty Crop Analysis Initiative in 2023. Individuals embrace researchers from MSU, Penn State College, Washington State College and Montana State College, in addition to Michigan corporations Exact Manufacturing and Proto-Tec Inc.
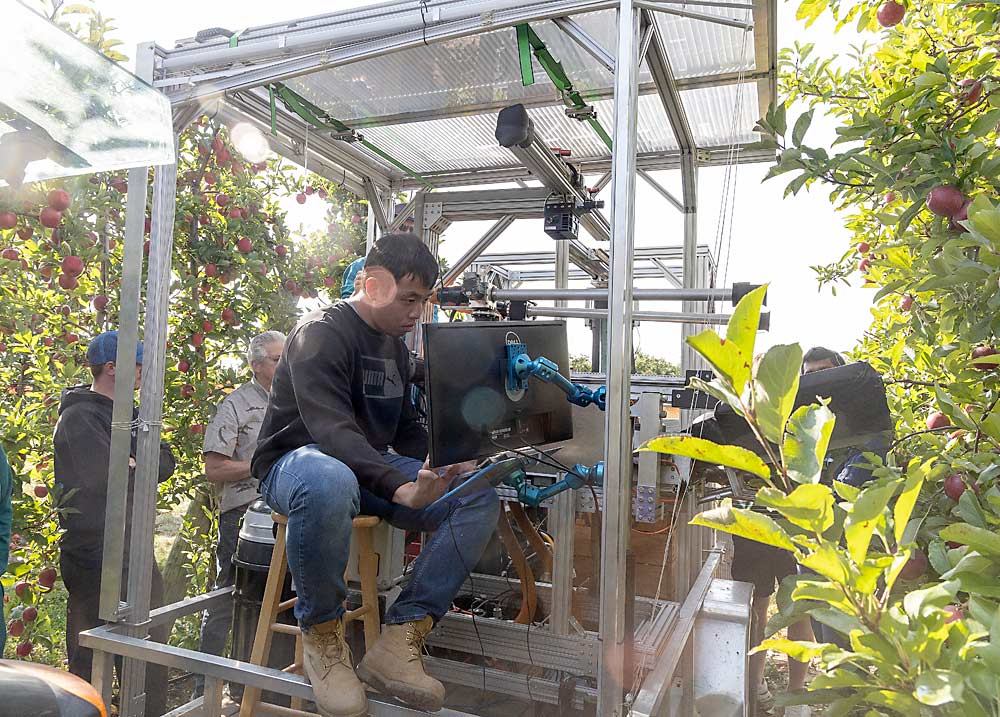
The venture’s mixture of robotic harvester and in-field sorter is novel and will assist remedy the rising downside of labor shortages, stated ARS Nationwide Program Chief Jonn Foulk, who spoke on the demonstration.
Grower Phil Schwallier preferred that the harvester induced little or no fruit bruising.
“The catching body and bin-filling equipment are very light,” Schwallier stated. “The apples seem like they are often put proper in your kitchen desk.”
The demonstration didn’t embrace the sorter, however when the machine is absolutely built-in, a conveyor will transfer the harvested apples to the in-field sorting module on the identical platform, the place it’ll kind the fruit into contemporary and processing bins. MSU researchers are analyzing apples picked by the harvester, to test for bruising, however Lu stated he’s assured the system handles fruit as gently as human pickers.
Lu’s harvester makes use of a vacuum system. Guided by a pc system, every robotic arm makes use of suction to connect the apple to the smooth rubber finish effector. The vacuum system runs consistently however ramps as much as full capability solely when the tip effector nears the goal fruit. As soon as the apple is connected, the vacuum mechanically ramps down once more, for larger power effectivity, he stated.
In contrast to gripper-style finish effectors, which require the proper method to an apple, the vacuum system can choose even when the method isn’t very best, stated Li of MSU.
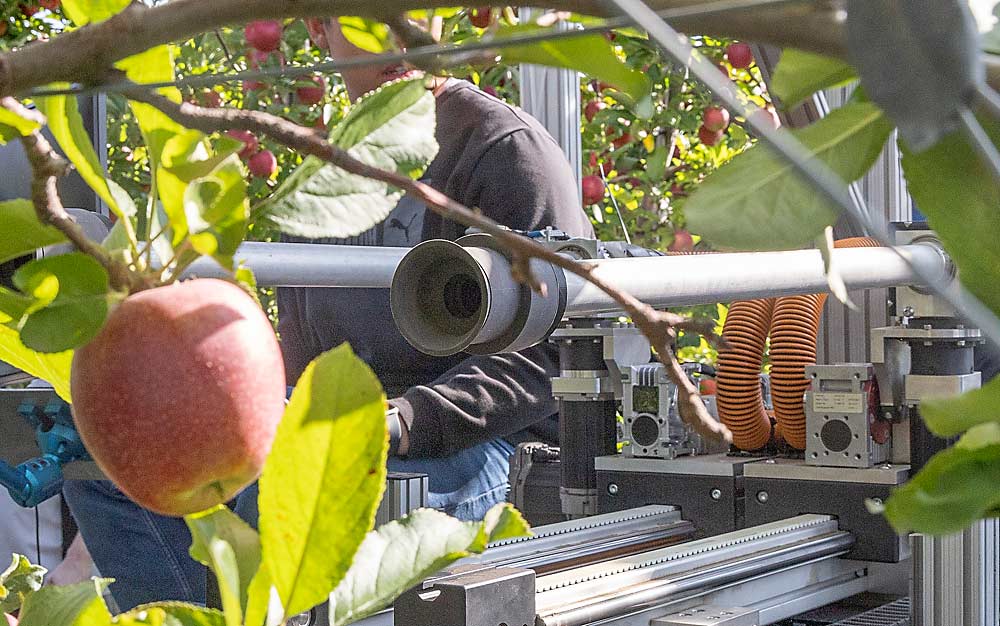
There are comparable harvester ideas being developed, however so far as the Michigan collaborators know, none embrace an automatic in-field sorting part.
Lu not too long ago noticed a vacuum-based robotic harvester developed by California firm superior.farm in motion in a Washington state orchard, and he made some comparisons for Good Fruit Grower.
The superior.farm harvester has six arms, in comparison with Lu’s eight, however every arm is extra dexterous than these of the USDA mannequin. When the superior.farm arms pull apples off a department, they generally pull off spurs, too. Lu’s vacuum arms suction the apples and twist them barely for simpler detachment, he stated.
There are also variations between the notion techniques that information the robotic arms. Superior.farm makes use of a stereovision system: two cameras near the tip effector. This offers extra correct data on fruit place, Lu stated. The Michigan prototype’s notion system is mounted on the mainframe, not the arms. It identifies all fruit inside a bigger working area after which makes use of that data to effectively information the arms. The digicam sits farther away from the cover, nonetheless, so details about the placement of particular fruits isn’t as correct, notably in the event that they’re lined by leaves or branches, he stated.
To take care of that, the Michigan analysis crew is growing an lively laser scanning algorithm to enhance the harvester’s means to localize goal fruits, Li stated. •